The
party was over. The world was shrinking. Glass tableware was "made
in Taiwan". The Swedish glass-industry bled. For BV the fight
for handicraft had begun. Solution: The Artist Collection.
The 1960s
/in terms of designing/may have seemed like one long honeymoon to
BV, but the 1970s entailed a long, hard struggle. The Åfors
factory, and others, were obliged to adapt/adjust to the new situation,
himself included. It was no longer possible to promote three new
services a year per designer. Household articles, such as vases
and bowls which before had been very profitable were no longer in
demand. Only a limited market for art glass and a wider one for
moulded glass remained. Bertil was already supplying both these
sectors, while desperately seeking an alternative to the increasing
mechanisation of the manufacturing process.
Many
glass-factory owners were contemplating automation at this time;
some had already implemented it. Åfors was not one of them.
On the other hand, the glassblowers at Kosta were obliged to work
in close proximity to the "industrial robot" that spewed
out party plates, snowballs and Xmas decorations, all round the
clock.
Erik
Rosen, former managing director of KostaBoda, admits that in the
long-term perspective investing in a machine of that size and expense
(i.e. 30 million Swedish kronor) had not been a good idea. In spite
of the advice from numerous consultants "our efforts with
the glass failed", he says. "The technicians had
no experience of handicraft, and were unable to adapt the automatic
process to our particular sphere of product."
The only
way out of the crisis, in Vallien's view, was: hand-made serial
glass that defied imitation. He forcefully maintained that if the
Swedish manual glass industry was to survive it had to back handicraft
and raise the artistic level. Throughout the 1970s he devoted himself
to improving working methods at the glass-factory. The artisans
were given a freer hand, and a greater personal responsibility in
the rationalisation of their work Particular phases of the manufacturing
process were facilitated by new equipment (and methods*) which Vallien
himself invented.
By 1976,
the work of renewal progressed. And now it was time to introduce
a new concept - the Artist Collection. This meant that an artefact,
while retaining its basic form would be "personalised"
by the artisans who handled it at the various stages of the manufacturing
process, thereby making imitation more difficult.
During
the 1970s Vallien was influenced by the ideas of the studio-glass
movement, which was gaining ground in America. There the emphasis
was on the unique artefact, the one-off, and greater freedom in
creation. He seized on these ideas to build up a rationalised production.
The outcome proved to be a great success, for him personally, and
for the Swedish glass industry.
One of
the first series within the Artist Collection was "Windpipes",
whose basic form originated in a number of unique clear-glass pieces
from the mid-1960s. These tall bottles with decorative surface applications,
and inlays of yellow and crushed lilac glass, are one of the most
popular series in the Artist Collection.
The receding
market for table glass naturally affected Vallien's own production.
Only six new collections left the drawing board during the1970s.
They were: Röhmer (1971), Old Boda (1975), Ballad (1975), Octave
(1977), H20 (1977), and Admiral (1979). The most successful of the
services was 'Octave' and a tone-setter for his subsequent glass
services in the '70s. 'H20' was inspired by laboratory/Chemistry
jars* and has a clean, almost ascetic design. Though not as long-lived
as Octave, it still is one of the most outstanding pieces in Vallien's
table-glass production.
|
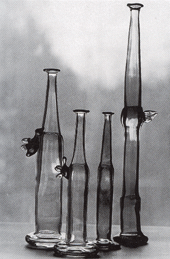
Windpipes.
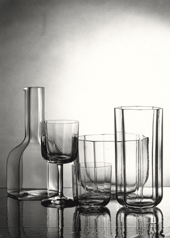
Octave,
1977.
H²O, 1977.
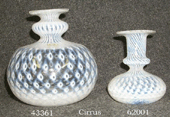
Cirrus,
1974.
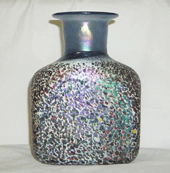
Bagdad,
1976.
|